Clinically pure breathing air
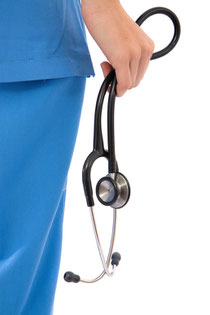
Due to the large volume of air that most hospitals consume, on-site production is normally the most practical and cost effective method of supply. This is accomplished by compressing ambient air with medical air compressors which have to be strictly maintained and ensure that the risk of contamination is minimised as much as possible.
Medical grade compressed air is used for a variety of applications, ie respiratory systems or processes, ventilation, substitute for nitrous oxide in anaesthesia, instruments, and pneumatically powered surgical tools. These compressed air systems normally have filters or special scrubbers to remove carbon monoxide and other pollutants, but this is not enough, as the system has to be tested and verified (or certified) on a regular basis.
Α reliable breathing air control system (Medical Breathing Air Control) protects patients against impure compressed air and complies with the production monitoring of Medical Air.
A stay in hospital is never a pleasant experience. The pain, the worries about health, the fear of an operation. Many people find it particularly worrying to depend on technical systems, such as the breathing air supply in the operating room or in the intensive care unit. The demands on the operation of the life-saving systems are correspondingly high. Therefore, the "European Pharmacopoeia" stipulates exact limit values for the composition of the so-called "Medical Air", meaning the compressed air which, in Medicine, is applied as the breathing air.
Safe production of Medical Air.
Breathing air is subject to medical laws.
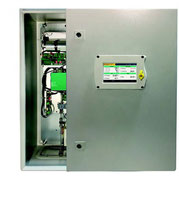
The Sigma 601 Series
• Particle concentration measurement
• Oil vapor measurement
• Dew point measurement
• Pressure measurement
For the control of the compressed-air quality in the medical field, we offer now a safe Medical Breathing Air Control system The Sigma 601 series. An uninterrupted service is as important as the purity of compressed air. High sensitivity of the system helps to immediately detect malfunction. Patients, as well as medical devices are thus protected at all times and the requirements on production monitoring are met.
The 601 Series Compressed Air Quality Analyzer, measures and monitors contaminants in real time, giving businesses confidence that its products and customers are protected.
The 601 series Compressed Air Quality Analyzer brings together state of the art technology in one easy to use package, allowing businesses to continuously monitor compliance to ISO 8573. The 601
monitors particle, dew point and oil vapor contamination across the full spectrum of ISO 8573 requirements including Class 0. Real time information can be retrieved from the 601 by SCADA systems
via MODBUS outputs.
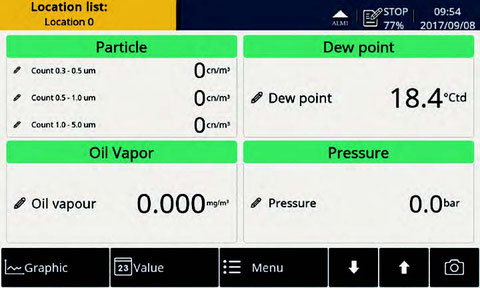
The integrated color touch screen display allows users to view all information locally.
The data logging function ensures records are kept intact. Alarm points can be set to trigger in the event that contaminants hit your selected limits. An optional external light or siren can
be fitted to the alarm.
The 601 is quick and easy to install, just connect the unit to power and the compressed air supply.
COMPRESSED AIR QUALITY ANALYZER Features / Benefits
• Particle concentration measurement
- Channel sizes: 0.3 ... 0.5, 0.5 ... 1.0, 1.0 ... 5.0 μm (A)
0.1 ... 0.5, 0.5 ... 1.0, 1.0 ... 5.0 μm (B)
- Laser particle counting technology
- Counting efficiency: 50% for smallest size 95% for all other sizes
• Oil vapor measurement
- Latest PID sensor technology
- Range from 0.003 ... 10.000 mg/m3
- High precision: 5%
• Dew point measurement
- Dual sensor technology (Polymer and QCM)
- Wide measuring range of -100° ... +20°C
- High precision of ±2°C
• Pressure measurement
- Measuring range 0.3 ... 1.5 MPa
- Accuracy of 1% FS
• Compressed air connection through 6 mm quick connect
• Ethernet (Modbus TCP), RS-485 (Modbus RTU) and USB interface
• Low purge air loss
• 100 ... 240 VAC power supply
• 5” color touchscreen with data logger
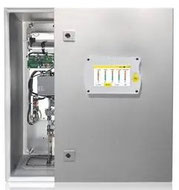
Sigma 606 24/7 Continuous Breathing Air Analyser
Sigma 606 is a wall mounted breathing air analyser for continuous monitoring in accordance with EN 12021. This instrument measures gas concentrations for oxygen (O2), carbon dioxide (CO2) and carbon monoxide (CO) in addition to dew point and oil vapour with programmable alarm settings for out of range alarms.
24/7 breathing air monitoring reduces the risk to users from quality issues that might occur between periodic testing and Sigma 606 system does not require regular user input to function reliably. Indeed, once the system is installed, the single pneumatic connection made and the power and signal connections established, the system can be relied on to provide alarm signals whenever the parameters exceed preset safe thresholds.
The easy to read touch screen display offers at-a-glance indication of the measured parameters in real time so that any operator can understand the air quality reading without fear of misinterpretation or needing specific training. The touchscreen menu system allows easy viewing and adjustment of the alarm settings and has an integral datalogger and PDF report generator for spot checks and specific testing.
Communication to BMS/SCADA systems or the dedicated S4A software is through Modbus TCP/RTU and there is an optional 4G dongle to enable wireless communication. Traditional local alarms can be wired through an optional 8 way relay expansion should that be needed.
Sigma 606 offers 24/7 breathing air user safety through continuous measurement from a self contained stand-alone system that only requires periodic calibration through exchange sensor modules that can be fitted by the user. There is no need for highly trained specialists or external contractors for this and the comprehensive instruction manual provides all the information and training needed.
Monitoring continuously
• O2 0-25%
• CO2 0-1000ppm
• CO 0-20ppm
• H2O -100 +20degC TD
• Oil Vapour 0.001 – 5.000mg/m3
• Pressure 0-16bar
• Modbus TCP/RTU Communication
• Programmable alarms
• PDF report generator
• Integral data logger
The S606 is perfect for monitoring breathing air quality continuously, but if you need mobile intermittent testing capability, the S605 is the perfect solution.